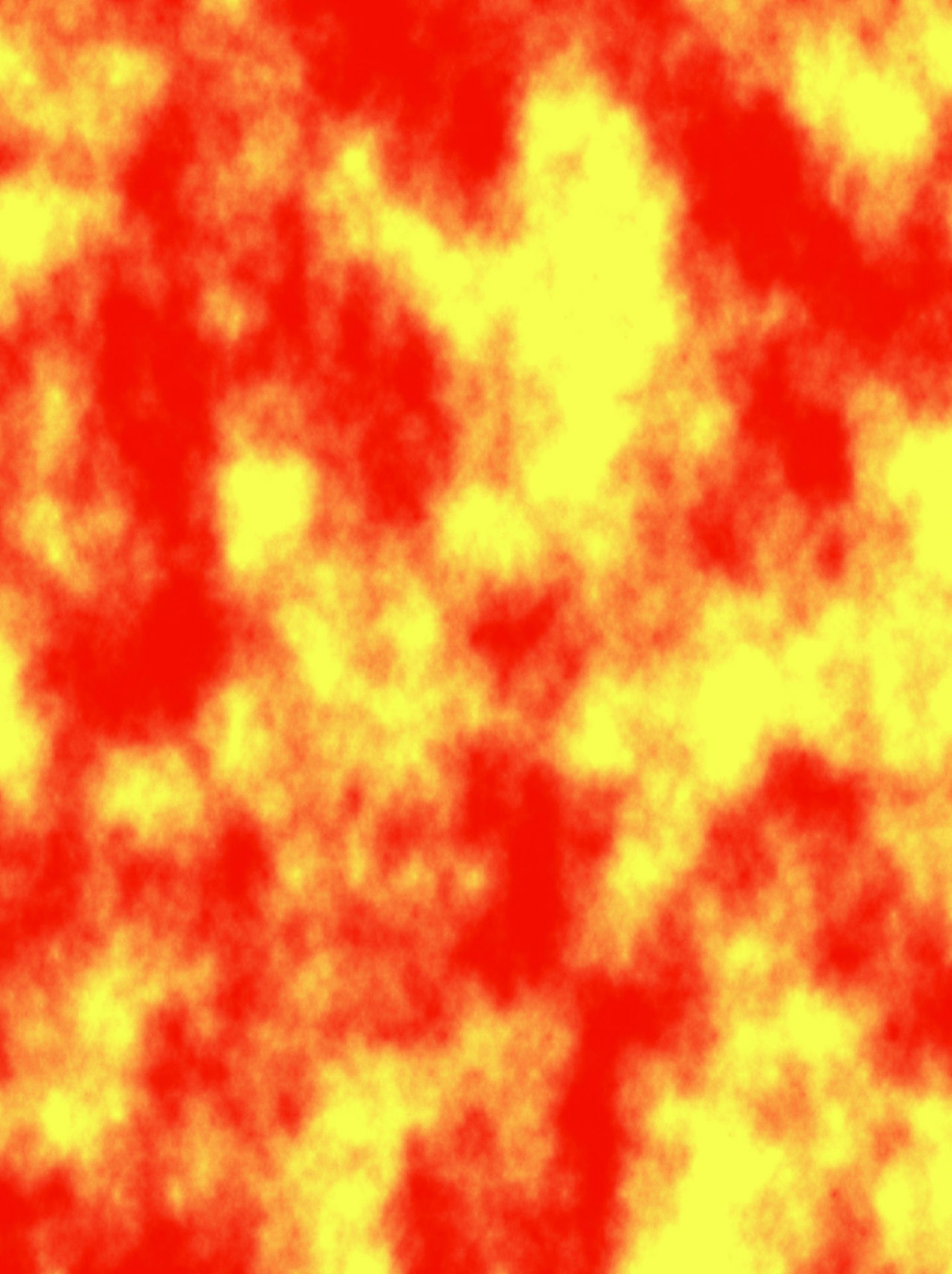
CIV Balzers
Vacuum Induction Furnace Balzers HU-40-25-40-04
Description, technical characteristics, components, methods of analysis of solidified melt

Induction furnace (in vacuum) - CIV (VIM) Balzers HU-40-25-40-04 is an metallurgical aggregate that can be obtained ferrous / nonferrous alloys from materials and alloys of commercial purity with low phosphorus content and sulfur, melting under the action of induction currents, effect of law Joule-Lenz.
The furnace is intended for lab-scale metallurgical experiments, to study of the interactions of materials at high temperature, inclusions, interaction with the refractory materials, etc.
It can be used for different kinds of technological processes i.e. melting, annealing, reduction of metals, sintering of bulk materials, infiltration of porous materials.
Processes performed under high temperatures and high vacuum ensure that no oxidation occurs and that the workpieces remain free of pores.
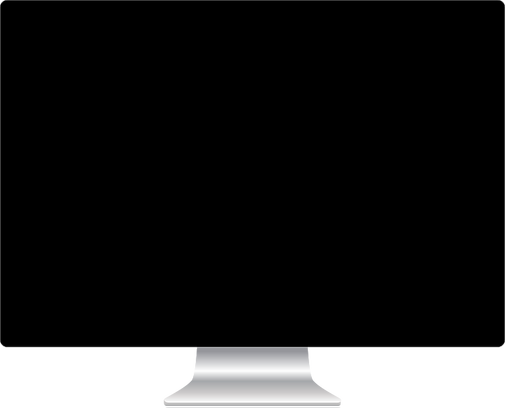

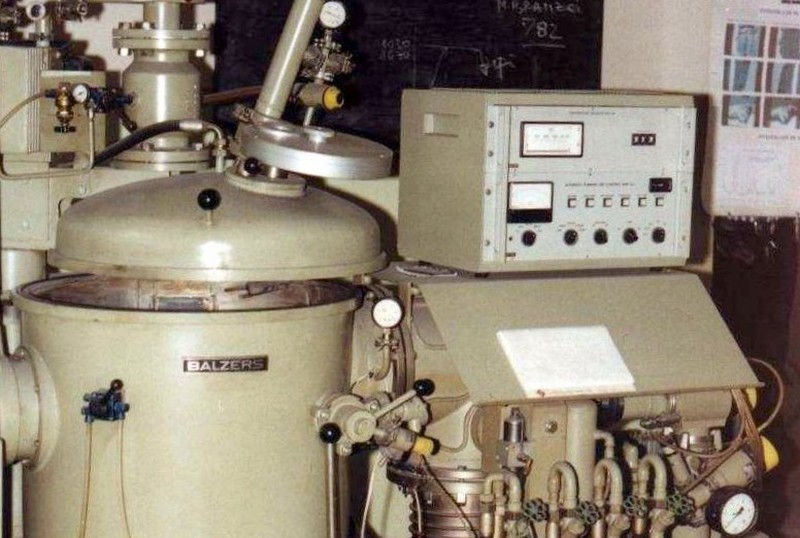
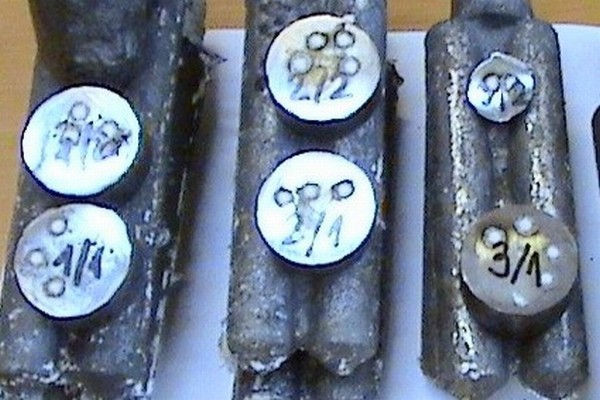

Main components of the furnace
Electric induction furnace with crucible consists of a stainless steel housing in which is a basic or acidic crucible (made by punching) placed inside a water-cooled copper coil - the inductor. The crucible is placed inside the copper coil, it placing it in turn in the vacuum chamber.
The inductor is made of copper pipe (by circulating water cooling) coils are placed in a single layer in the form of solenoid. Presents also intended to strengthen and stiffen the crucible, being constructed in various technological options.
The converter is central power system of induction furnaces, being of two types: parallel resonant converter and resonant converter in series, the most common being the converter with resonance in series.
The supply leads can be rigid or flexible connections, the second system, with losses of up to 5% of the active power of the oven being used much because of the simplicity of the solution.

Vacuum induction furnace Balzers HU-40-25-40-04
The tilting mechanism is operated manually or hydraulically. In principle, to evacuation with it, furnace rotates around an axis that runs beneath the discharge gutter, system allows shortening jet steel, this reduces the phenomenon of secondary oxidation.
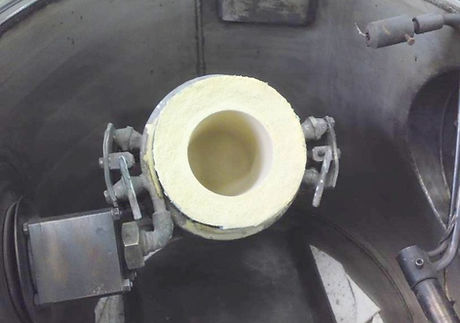
Furnace crucible is made of granular masses embossing basic (magnesia) or acidic (silica) by beating, outside tank sealing (to limit interstitium between crucible and inductor) by the dry process or wet.
It must withstand high temperatures during the drafting process (over 1600 °C), due to mechanical loading weight of solid or metal bath and chemical corrosive action of the slag and molten metal.
In principle, it uses preformed based MgO spinel crucibles and dry mass refractory type Rodacor Mix 016, material chemically neutral, forming neutral spinels at temperatures between 1650...1700 ºC, accompanied by increases in volume that helps compaction and consolidation refractory lining.
Refractory lining of induction furnace Balzers before sintering
If it works at lower temperatures of 1650 °C is recommended every week to make a heated above 1650 ºC for restoring sintered layer and increase the lifespan of lining. The maximum temperature is 1750 °C. Stamping runs in accordance with the working procedures for dry refractory materials and sintering is linear with a speed of 200 ºC / h.
Main technical characteristics of the furnace
Tree-phase AC power supply
-
Power consumption 48 kVA
-
Voltage 3x380 V
-
Frequency 50 Hz
Output Characteristics
-
Nominal power 40 kW
-
Nominal voltage 250 V
-
Rated frequency 4 kHz
-
Total reactive powe: 618 kVA
Operating areas
-
Power: average 0...44 kW
-
Voltage: average 0...260 V
-
Frequency: average 3...4,05 kHz
-
Continuous current: 5...89 A
Transformer
-
Nominal capacity at 4 kHz: 100 kVA
-
Primary/secondary voltage: 250/250 V
General specifications
-
Cooling water flow rate
- without consumption unit 22,5 l/min.
- with consumption unit 27,5 l/min.
-
Max. cooling water temperature inside the coil 300ºC
-
Inner cooling water pressure:
minimum 3 barr, maximum 6 barr.
Capacity crucible:
-
max. 10 kg liquid steel.
By selecting optional output voltages of average frequency converter is possible that all processes of melting and sintering, both in atmosphere and vacuum, with or without inert gas present in furnace chamber.
Furnace capacity, depending on the volume crucible for liquid steel
a. Large crucibles
● Dimensions:
Dint. = 9,5 cm; Hint. = 21 cm; V = 1488 cm³ ≈ 1,5 dm³
● Maximum filling capacity:
Dint. = 9,5 cm; Hint. = 18 cm; V = 1, 275 dm³
● Steel batch maximum weight :
Motel = V x δ = 1,275 x 7,8 ≈ 10 kg
b. Small crucibles
● Dimensions:
Dint. = 5,5 cm; Hint. = 12 cm; V = 285 cm3 ≈ 0,285 dm³
● Maximum filling capacity:
Dint. = 5,5 cm; Hint. = 9 cm; V = 0,214 dm³
● Steel batch maximum weight:
Motel = V x δ = 0,214 x 7,8 ≈ 1,66 kg

Crucibles of refractory materials used in the production of metallic materials
The crucibles are made from high purity refractory materials with refractory high, capable of withstanding temperatures of up to 1800ºC. Depending on the metal material to be produced, they are made of alumina, zirconia and magnesite.
Casting machine
Casting machine has been designed taking into account the experimental conditions, and production capacity of induction furnace. To this end it was taken into account on the destination machine, namely:
-
ingot mold to obtain ingots for plastic deformation (forging, rolling, etc.);
-
ingot mold to obtain specimens for testing the mechanical properties of cast alloys.

Ingot molds to obtaine casting ingots for plastic deformation (forging, rolling, etc.) presents round and polygonal (hexagonal) sections, in order to study the influence of the ingot section in the quality of products metal deformed. To reduce blowhole ingots, given that casting is performed directly, ingot molds are inversely tapered.
To calculate the sizes of the ingot molds was considered the furnace production capacity, furnace fitted constructively with two types of inductors: one with the maximum capacity of 2 kg liquid steel, and one with the maximum capacity of 10 kg liquid steel, which is why ingot molds have the ability 6, 7 and 10 kg respectively liquid steel.
Also, the laboratory is equipped with ingot molds for flat casting products for use in various technical applications.
Cast iron ingot molds for casting metallic materials in the laboratory ERAMET
Ingot molds for obtaining molded test specimens were designed and executed in view of the possibility of mechanical characterization of metallic materials in two types and sizes, namely:
-
standard samples for ingot molds in which to obtain size round bars Ø 22 x 165 mm;
-
reduced samples for size round bars Ø 14 x 120 mm.
To ensure obtaining materials without blowhole, ingot molds were designed with a casting funnel to have the role of exterior part of ingot.
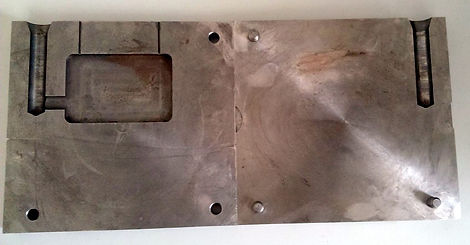
Ingot molds for flat casting products
Since the final shape of molded products must be reconciled cylindrical, ingot molds for specimens were taken from two semi ingot molds separation lengthwise, so as to allow extraction facility of castings parts.

Ingot mold for standard specimens

Ingot mold for casting small specimens
Capacity ingot molds for standard specimens or reduced, depending on the internal volume for liquid steel:
a. Ingot mold for standard specimens
● Dimensions:
D = 2,2 cm; H = 15,5 cm; V = 59 cm³ ≈ 0,059 dm³
● Specimen weight:
Motel = V x δ = 0,059 x 7,8 ≈ 0,46 kg
● Size tank:
L = 6,2 cm; l = 3,6 cm; H = 1,5 cm;
V = 33,48 cm³ ≈ 0,035 dm³
● Tank weight :
Motel = V x δ = 0,035 x 7,8 ≈ 0,273 kg
● Total weight of the standard specimen:
2 x 0,46 + 0,273 ≈ 1,2 kg
b. Ingot mold for casting small specimens
● Dimensions:
D = 1,4 cm; H = 12 cm; V = 18,46 cm³ ≈ 0,0185 dm³
● Specimen weight:
Motel = V x δ = 0,0185 x 7,8 ≈ 0,145 kg
● Size tank:
L = 6 cm; l = 3,6 cm; H = 1,5 cm;
V = 32,4 cm³ ≈ 0,0324 dm³
● Tank weight:
Motel = V x δ = 0,0324 . 7,8 ≈ 0,253 kg
● Total weight of the small specimen:
2 x 0,145 + 0,253 ≈ 0,543 kg
c. Ingot mold (chill) for sampling is made of solid copper in which it is practiced a circular footprint with a diameter of 40 mm and depth of 20 mm and allows to obtained cylindrical samples for examination, on the spectrometer, chemical composition of obtained alloys.

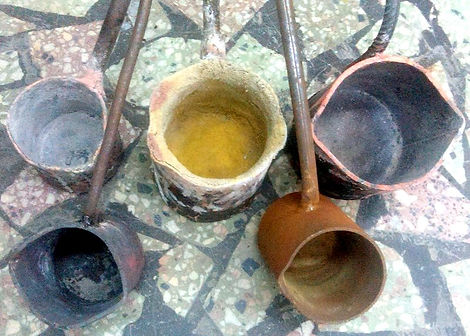
Ingot mold (chill) for sampling
Molding ladles of different capacities
Molding ladles of liquid alloy are tailored to induction furnace capacity and have capabilities 2...10 kg liquid steel. The ladles have different capabilities and are used for casting liquid alloys in ingots or parts.
Nothing better captures the atmosphere of a particular place than a video. That is why we provide a few clips of presentation of laboratory activity ERAMET, videos are always so most awaited, and most appreciated.
Conducting various metallurgical experiments with Vacuum Induction Furnace Balzers HU-40-25-40-04 in the ERAMET Laboratory
During the experiments, can be extracted samples and additions can be made and dissolved oxygen can be measured with a lance, without damaging the furnace atmosphere or vacuum. The furnace is equipped with a pressure control with mass flow controllers and thermocouples, and sends data to a PC with dedicated visualization and software recording the results.
Temperature is measured continuously and the furnace is gas-tight so that experiments can be conducted under protective (Ar or N2), active (CO/CO2 or air) atmospheres or vacuum.
The partial oxygen pressure (pO2) can be set by means of two mass flow controllers that control CO/CO2-ratio.
The analysis of solidified melt
For qualitative and quantitative metallographic analyzes of examined material, the solidified melt in the mold is cut into slices perpendicular to the axis of the ingot casting.
Metallographic samples, after cutting, it locks in polymer resin. It then performs operations grinding and polishing standard, using emery paper and diamond paste, thereby achieving an acceptable quality of cross sections.
To improve the contrast of images electron microscope SEM taken from the sample structure molded, cross sections are coated with a thin layer of carbon, approximately 20 nm.
The assessment of the molded samples quality is conducted using methods of optical and electron microscopy. Optical microscopy is used mainly as a check of the sample quality before investigations by electron microscopy or spectroscopy.
The most important methods for observation and elemental analysis of the experimental alloys was scanning electron microscopy (SEM) and X-ray spectrometry.
A special method of TEM sample preparation in a form of thin lamellae for transmission electron microscopy using focused ion beam (FIB), facility used for solidified melts.
For investigations are used existing equipment in the laboratories of Research and Expertise Center for Special Materials CEMS-UPB, within Faculty of Materials Science and Engineering:
Lab.01 Laboratory metallographic samples preparation
Lab.02 Laboratory Optical Microscopy
Lab.03 Laboratory Scanning Electron Microscopy (SEM)
Lab.04 Laboratory Transmission Elec. Microscopy (TEM)
Lab.05 Laboratory chemical analysis by spectrometry